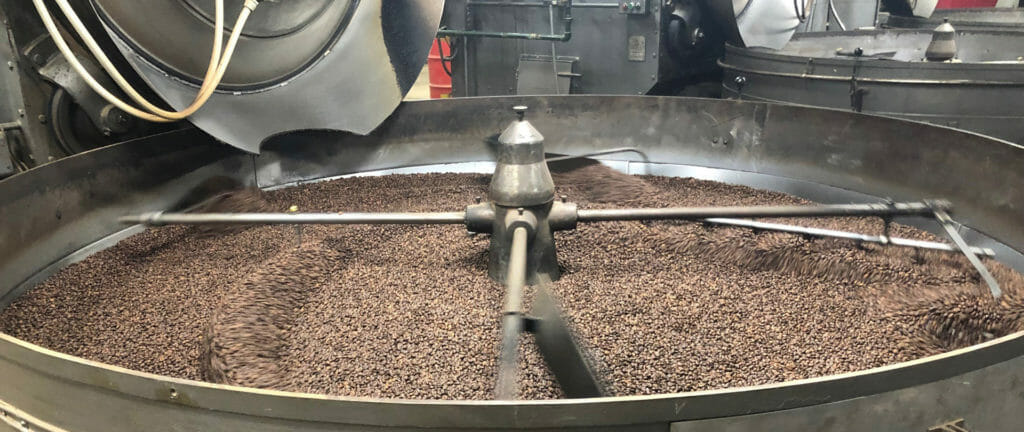
Operations
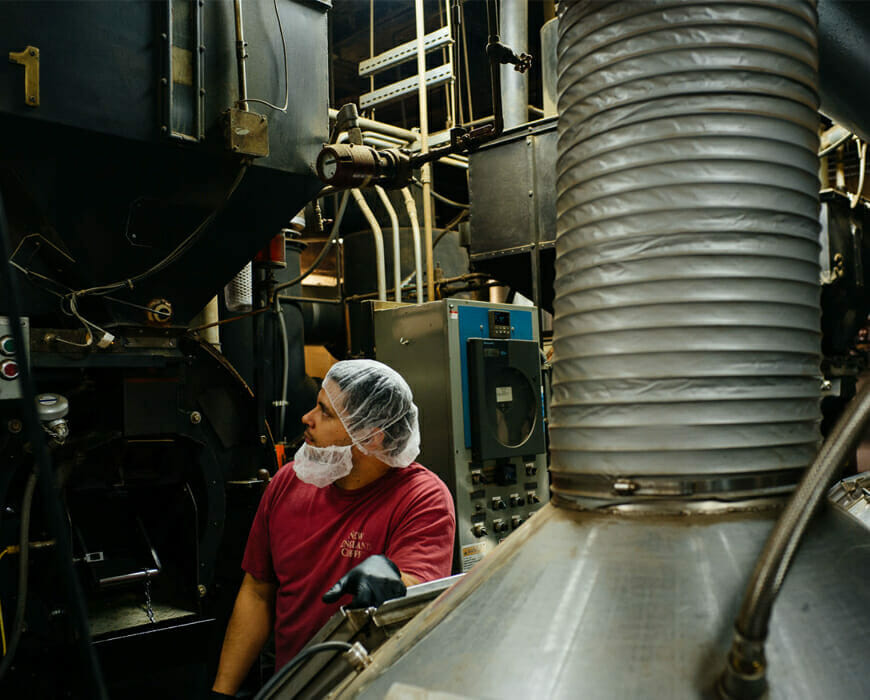
Climate and Energy
Our carbon footprint is dominated by electric and natural gas use associated with processing, packaging and distributing coffee, tea, mayonnaise, baking flour and sauces. We’re reducing electric and natural gas use and exploring more fuel-efficient fleet vehicles, renewable energy in our facilities and other GHG-reducing investments.
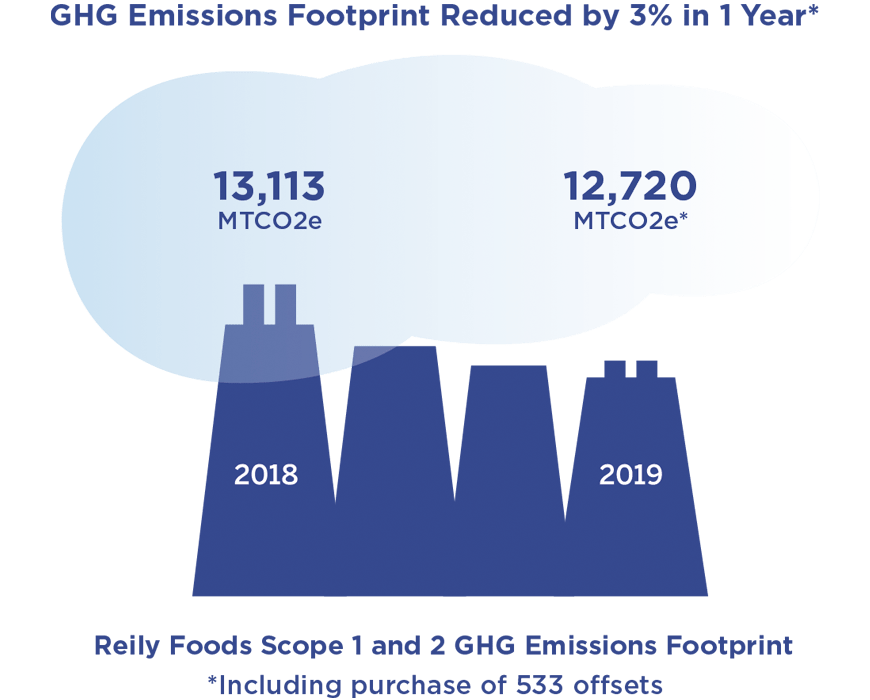
Our 2025 goal: 20% reduction in Scope 1 & 2 emissions (2018 BASELINE)
Our Progress
- High-efficiency light replacement initiative
- New light motion sensors
- High-efficiency nitrogen generators & compressors
- Battery operated, rechargeable forklifts
- Ongoing engineering work on coffee processing equipment
- Energy Star certified corporate headquarters
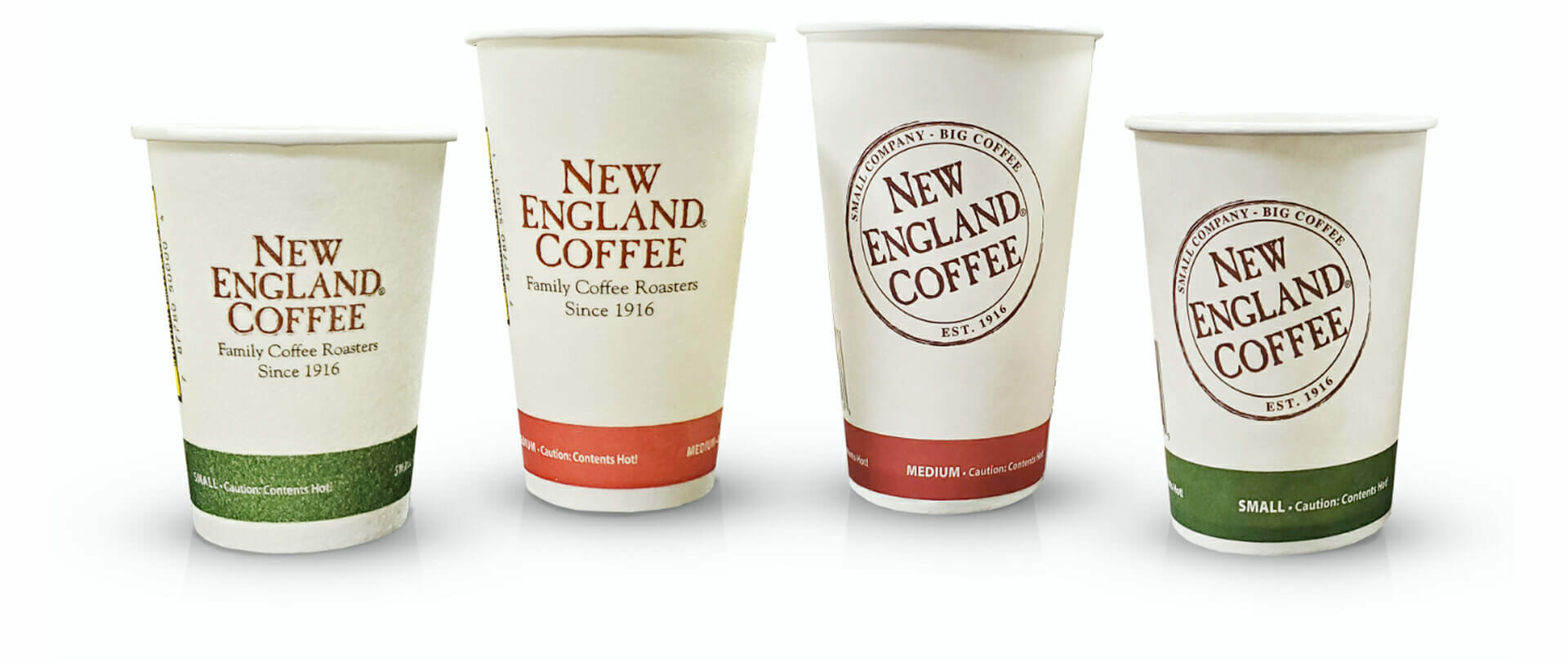
Tripling Efficiency at New England Coffee
We rely on nitrogen (produced using compressors) to displace oxygen to maintain coffee freshness in packaging. Our maintenance manager partnered with the local utility to evaluate the efficiency of existing technology, resulting in an investment in new nitrogen compressors that are three times more efficient.
“Our coffee products rely on premium raw materials and complex engineering. Investing in efficient production equipment meaningfully impacts our ability to achieve our high quality standards.”
JOE SARETTE
MAINTENANCE MANAGER, NEW ENGLAND COFFEE
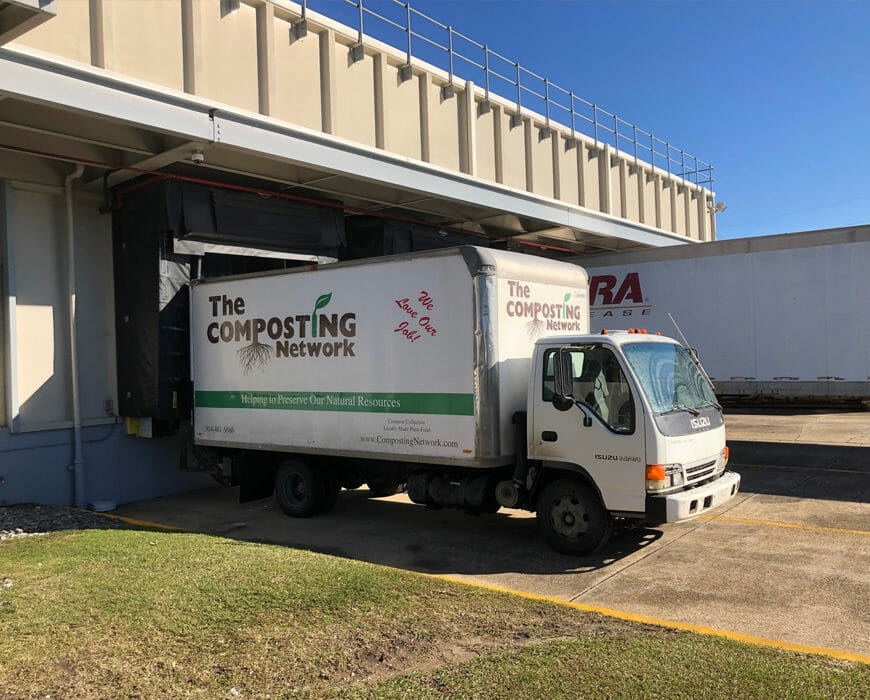
Waste Reduction
Waste management offers a clear path to sustainability goals and also to cost savings and quality assurance. We’re improving our already robust recycling and reuse programs by focusing company-wide on diverting more waste from landfill to reuse.
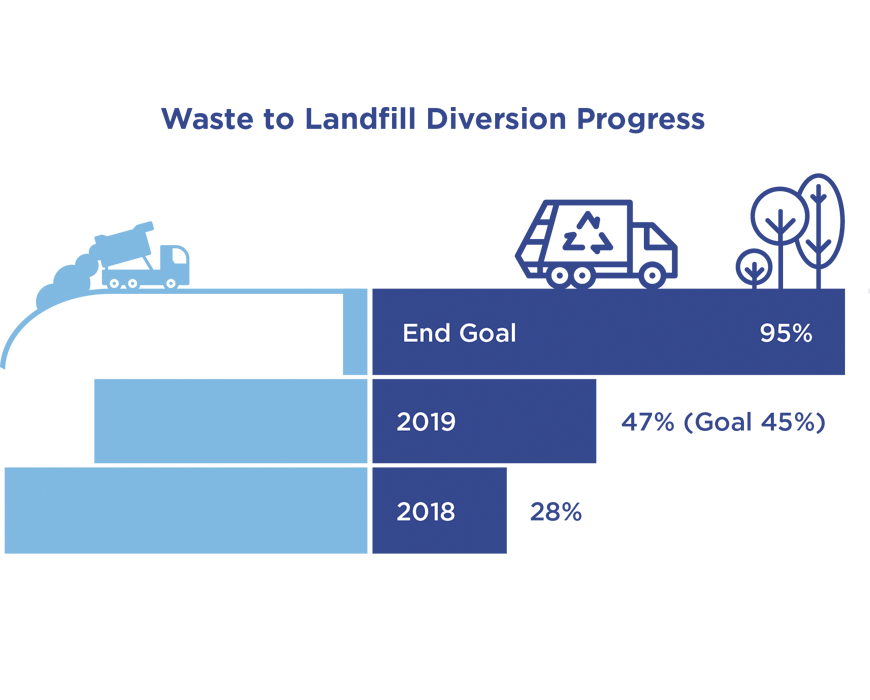
Our 2025 goal: 95% waste to landfill diversion (2018 baseline)
Our Progress
- Recycling programs at all facilities including commonly recyclable materials: corrugate, PET plastic, metal & paper
- 100% of mayo oil is reused
- 100 tons of burlap coffee sacks are repurposed by small businesses for uses ranging from composting to oyster farms to packing material for concrete birdbaths
- Total of all recycled and reused materials is now 900+ tons
Innovating for a Circular Economy
The Reily Foods Company’s Knoxville plant was faced with an organic waste issue. For years, the “chaff” removed from roasted coffee beans and half-filled plastic mayonnaise jars produced during switchovers ended up in the landfill.
SOLUTION
Sevierville Solid Waste now mixes Reily Company’s organic waste, along with solid waste from the Smoky Mountain National Park, with biosolids in large, turning digesters. After 3 days, all of the organic material becomes compost. Inorganic material is screened out, and the resulting Grade A compost is made available to the community at no charge to support landscaping, soil amendments and erosion control.
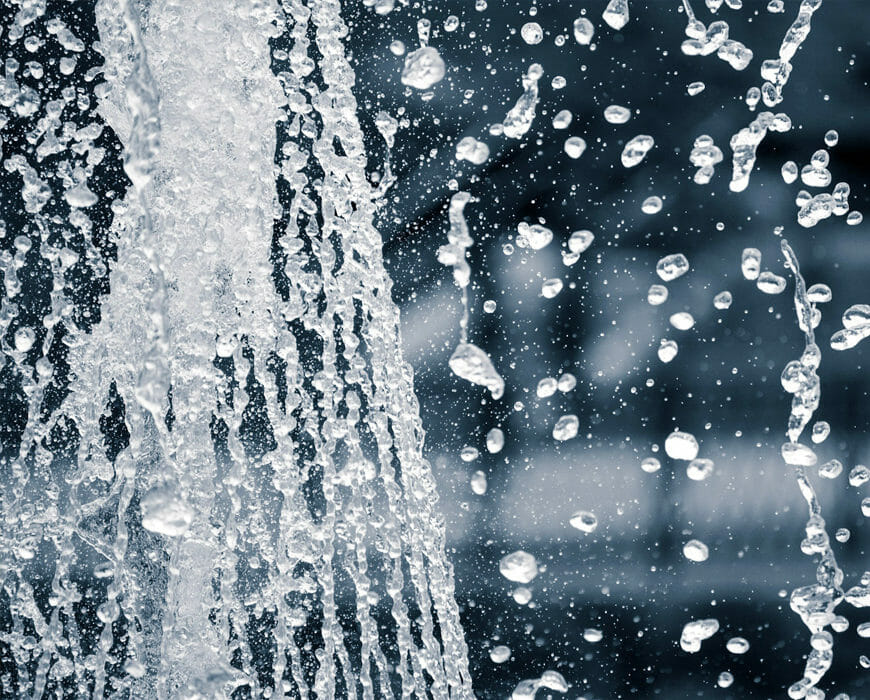
Water Use Efficiency
Our highest water use is in our Knoxville, Tennessee facility, for mayonnaise production. While our facilities are not located in water-scarce regions and our overall usage is relatively low, we’re still finding ways to improve.
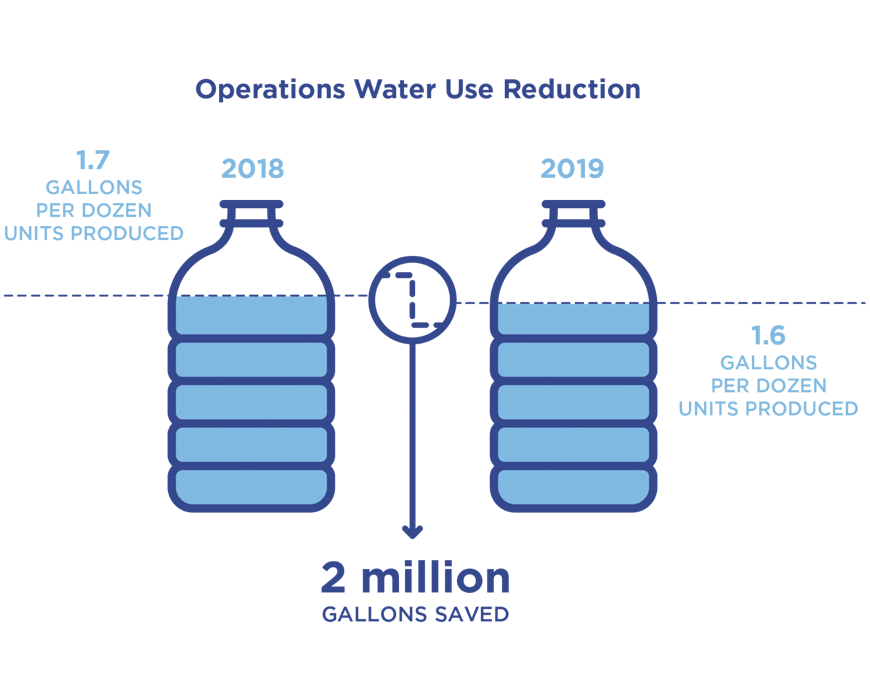
Our 2025 goal: 5% reduction in purchased water per unit of product (2018 baseline)
Our Progress
- 2 million gallons of water saved in production (2018 to 2019)
- Water-use efficiency practices adopted for grounds maintenance
- Exploring water-saving faucets and toilets
- Exploring more opportunities to reduce water use in production